ПОЛИСТИРОЛ -
PS
(бакелит, стирон, фостарен, эдистер,
VESTYRON,
POLYSTYROL) Полистирол получают блочной, эмульсионной и
суспензионной полимеризацией стирола (винилбензола) - жидкого
синтетического продукта. Рассмотрим подробнее суспензионный метод:
суспензионная полимеризация осуществляется по периодической схеме в
реакторах объемом 10-50 м3, снабженных мешалкой и
рубашкой обогрева. Стирол суспендируют в деминерализованной воде,
используя различные стабилизаторы эмульсии; инициатор полимеризации
растворяют в стироле. Процесс ведут при постепенном повышении
температуры от 40 до 1300С под давлением в течении 8-14
часов. Из полученной суспензии полистирол выделяют
центрифугированием, после чего его промывают и сушат. Этот процесс
удобен и для получения сополимеров стирола. Этим же методом в
основном производят и пенополистирол (коробочки для фасовки яиц,
подносы и лотки для расфасовки свежего мяса, рыбы). Товарный
полистирол выпускается неокрашенным и окрашенным, в порошке и в
гранулах. Неокрашенный полистирол после плавления и охлаждения -
прозрачный и бесцветный материал.
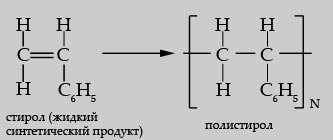
Для получения
материалов, обладающих более высокими теплостойкостью и ударной
прочностью, чем полистирол используют смеси последнего с другими
полимерами и сополимеры стирола, из которых наибольшее значение
имеют блок и привитые сополимеры, так называемые ударопрочные
материалы (АБС-пластик, УПС- ударопрочный полистирол).
УПС (HI-PS - полистирол высокой ударной
прочности). УПС
получают привитой сополимеризацией стирола с полибутадиеновыми или
бутадиен-стирольными каучуками. Структурно УПС представляет собой
трехфазную систему, состоящую из полистирола, гель-фракции привитого
сополимера и каучука с привитым стиролом в виде частиц с размером до
1-5 мкм, равномерно распределенных по объему УПС. Присутствие
каучука существенно замедляет рост микротрещин, что и повышает
прочность материала. Ударопрочный
полистирол более гибок, имеет большую ударную прочность, но меньшую
прочность при растяжении и термическую стойкость, чем
немодифицированный полистирол.
Ударопрочный полистирол - превосходный
материал для получения различных изделий методом
термоформования. Введение в ПС
синтетических каучуков, уменьшая хрупкость, снижает прозрачность ПС.
Основные свойства УПС: твердый, жесткий, плохо ломающийся,
непрозрачный (учитывая содержание бутадиена), цвет молочно-опаловый,
может быть окрашен во все цвета, способность поглощать влагу большая
чем полистирола.
Свойства полистирола: степень полимеризации
N=600-2500;
ММ = (80-100)*103; характеризуется высокой прозрачностью
(светопропускание до 90%); температура стеклования (температура
размягчения) 80-1000С; диапазон технологических
температур 190-2400 С; температура самовоспламенения 4400С;
плотность 1,05 г/см3; водопоглощение 0,05-0,1
(предварительная сушка необходима только при неблагоприятном хранени);
усадка (при изготовлении изделий) 0,3-0,6%.
Химические свойства: Полистирол растворяется в собственном мономере, ароматических и
хлорированных углеводородах, сложных эфирах ацетоне, не растворим в
низших спиртах, алифатических углеводородах, фенолах, простых
эфирах. Обладает низким влагопоглощением, разрушается
концентрированной азотной и ледяной уксусными кислотами.
Физические свойства: Полистирол – термопластичный полимер линейного строения. Аморфный,
прозрачный хрупкий продукт. Для него характерны легкость
переработки, хорошая окрашиваемость в массе и очень хорошие
диэлектрические свойства. Легко склеивается. Термодеструкция
начинается при 2000С и сопровождается выделением
мономера.
Эксплуатационные свойства: Полистирол не токсичен. Недостатки – хрупкость и низкая
теплостойкость; сопротивление ударным нагрузкам невелико. При
температурах выше 600С снижается термоустойчивость. На
воздухе при УФ-облучении полистирол подвергается старению:
появляется желтизна и микротрещины, происходит помутнение,
увеличивается хрупкость.
Полистирол
перерабатывают всеми известными способами при 190-2400С.
Применяют как конструкционный, электроизоляционный (пленки, нити),
декоративно-отделочный материал в приборо и машиностроении, для
изготовления изделий широкого потребления. Ориентированный ПС
толщиной менее 75 мкм используют для "окошек" в картонных
упаковочных коробках. Более толстые пленки используются для
получения стаканчиков для торговых автоматов, подносов для
фасованного свежего мяса, с тем, чтобы видеть при покупке обе
стороны упаковываемого продукта.
Вспененный
полистирол обладает высокой
жиростойкостью,
является прекрасным
теплоиэолятором.
Применяется для изготовления различных упаковочных изделий методом
термоформования (прокладки в ящики для
яблок, коробочки для фасовки яиц, подносы и лотки для расфасовки
свежего мяса, рыбы).
Основные параметры
литья под давлением:
Температура
переработки:
Температура, 0С |
Съема
изделия |
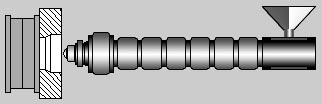 |
Сушки
|
TП |
TС |
Т1 |
Т2 |
Т3 |
Т4 |
TЗАГ |
70 |
15-50 |
190-230 |
190-240 |
190-240 |
170-220 |
160-200 |
30-50 |
80 |
ТП - температура прессформы;
TC -
температура сопла;
T1 - температура первой зоны
обогрева;
T2 -
температура второй зоны обогрева;
T3 -
температура третьей зоны обогрева;
T4 -
температура четвертой зоны обогрева;
TЗАГ -
температура зоны загрузки материала;
Предварительная
сушка необходима только при неблагоприятном хранени,
длительность сушки составляет 1 час.
Параметры процесса литья:
Давление впрыска: высокое 1000-1400 бар
(100-140 бар - на манометре термопластавтомата).
С учетом максимального давления впрыска на термопластавтомате - 1400 бар.
Скорость впрыска: обязательна высокая
скорость; при понижении скорости впрыска снижается прозрачность
полистирола.
Давление выдержки (подпрессовки): 30-50% от
давления впрыска (невысокое, но достаточное, чтобы не "отбрасывало"
шнек внутренним довлением материала в прессформе).
Время выдержки (подпрессовки): Учитывая
высокое внутреннее напряжение материала, а также низкую величину
усадки полимера, рекомендуется небольшое время выдержки до 20% от
времени охлаждения.
Подушка (остаточная): 2-6 мм, в зависимости от
объема дозирования; больше объем - больше подушка.
Время охлаждения: должно быть настолько
длительным, чтобы литое изделие остыло до беспроблемного извлечения
из прессформы; определяется толщиной стенок изделия, температурой
стенок прессформы, температурой расплава материала.
Обороты шнека: высокие, чтобы время
пластификации уложилось в период охлаждения изделия; нет
необходимости набирать дозу материала быстрее, чем закончится время
охлаждения изделия.
Противодавление: 100-250 бар (10-25 бар по
манометру термопластавтомата); при более низких значениях может
появиться пригар (черные шлиры на поверхности и мелкие пузырьки
воздуха ) используется в основном для
стабильного дозирования и гомогенизации расплава,
и для равномерного распределения красителя в материале; нет необходимости дальнейшего увеличения противодавления
во избежание остановки шнека и прекрашении процесса набора дозы. |